How Spray Foam Roofs are applied versus Membrane Roofs
Aside from the physical properties, one of the largest differences between Spray Foam Roofing and other types of membrane roofing is the way that they are applied. TPO, for example, comes in pre-manufactured rolls that are then rolled out on the roof, adhered or mechanically fastened, and the seams are hot air welded together.
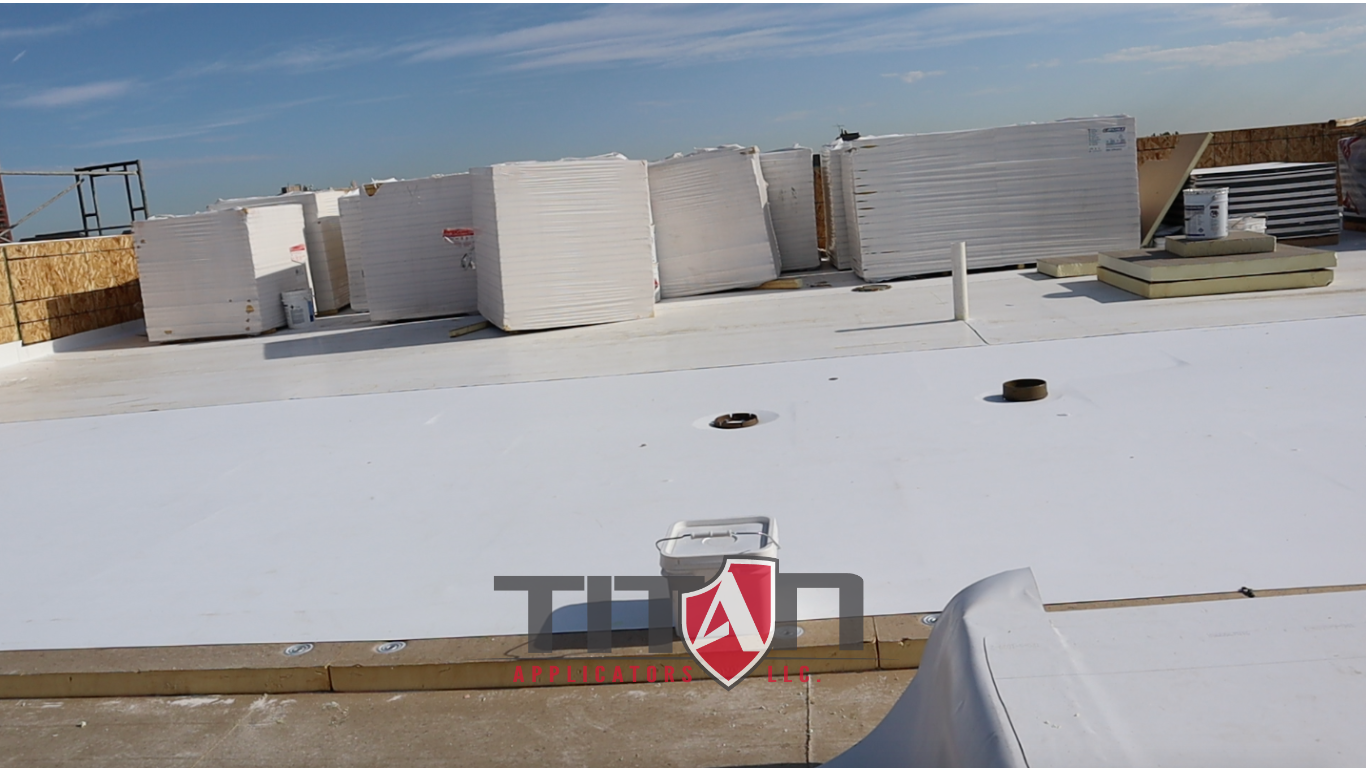
Spray Foam on the other hand, is ultimately manufactured on the roof by the installer. Spray foam (SPF) arrives at the job site as an “A” and “B” chemical which are then mixed together using specialized equipment. Spray foam is sprayed at a 1:1 ratio, meaning that for every 1 part of “A”, there needs to be a corresponding 1 piece of “B.” Being that the Isocyanate (A side) and the Resin (B side) are different viscosities, this blend is controlled by temperatures and pressures. It is very important that the installer is familiar not only with the chemical, but with his or her equipment as well. An off ratio blend can cause a mess on the roof, resulting in poor cell structure and a finished product that won’t keep the water out of your building and won’t stand up to the test of time.
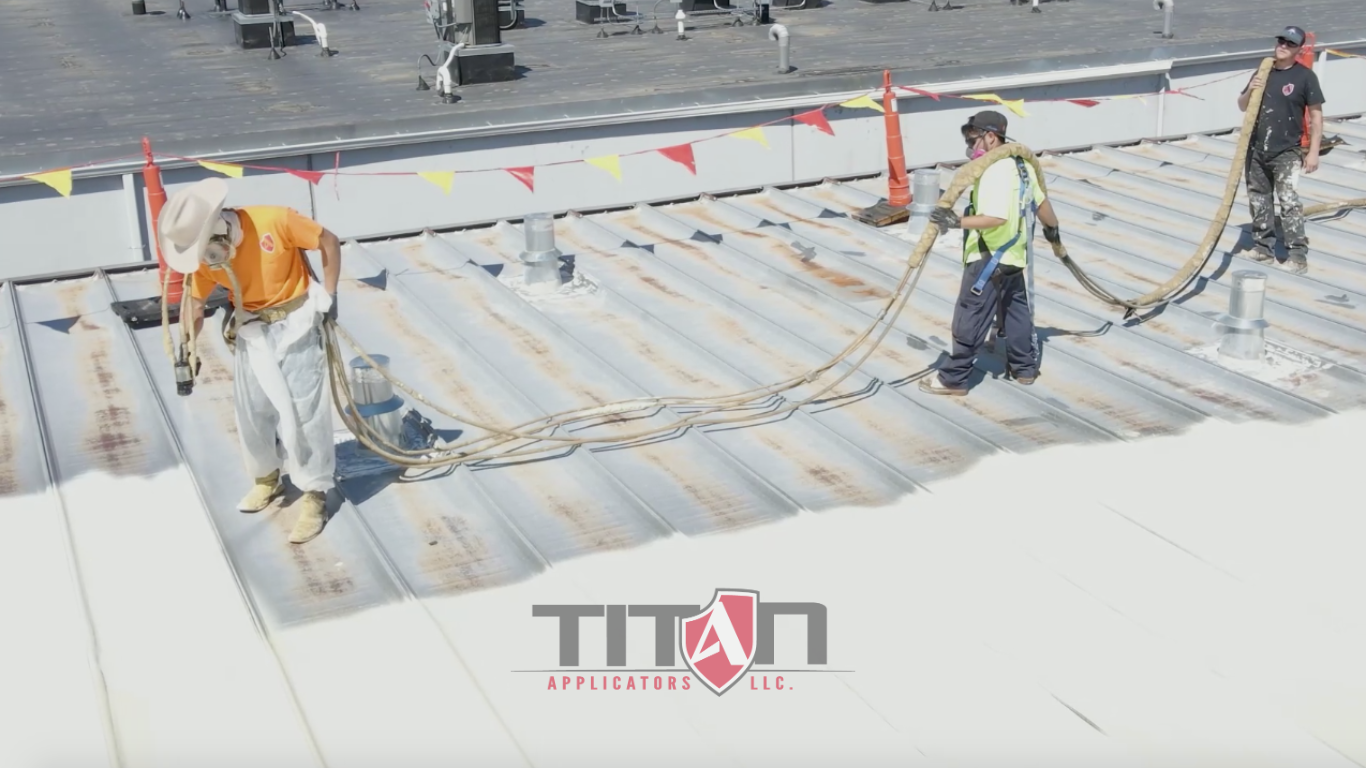
The installation process for SPF roofing gives it a few advantages; Number 1 being that because the end product is manufactured in the field, SPF will conform and fit just about any shape and structure and Number 2, SPF roofing is one of the only true seamless roofs. Because of the nature of foam, it is also self flashing, which reduces labor costs and the risk of leaks due to installation. Because it is sprayed directly onto the deck in liquid form, SPF can also offer a more workable product on different shapes, angles, and detail work.
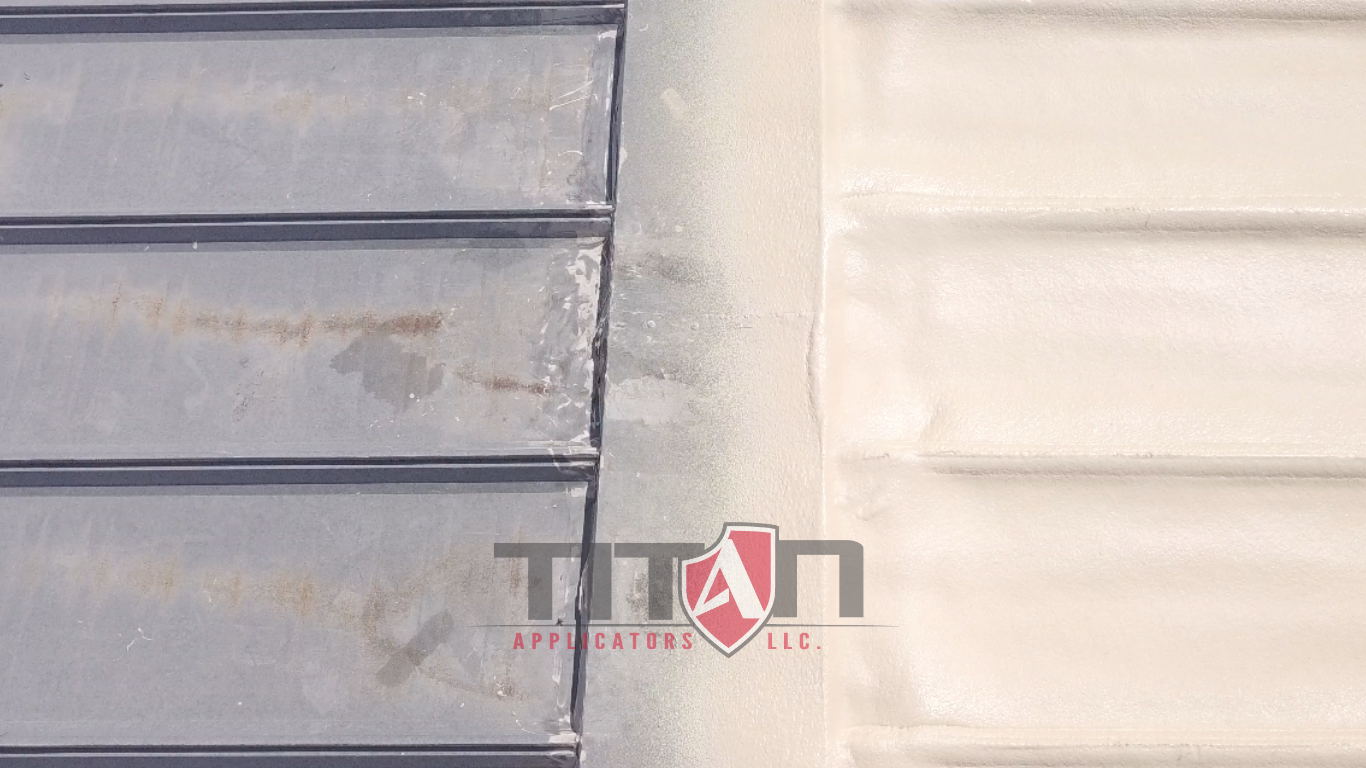
Before the installation of a spray foam roof can even begin, the roof will need to be free of all dirt, dust and contaminants. First, the polyurethane foam is sprayed down onto the existing roof. Since this foam can adhere to nearly any surface, it can be installed on most roof types. These foam roofs are custom made to each building, much different from piecing together separate parts for a membrane roof. After the layer of polyurethane foam is sprayed, elastomeric silicone or acrylic coating is then applied. Care will need to be taken during installation, as there is always a possibility of overspray.
How Do You Install Membrane Roofs?
For a membrane roofing, typically a cover board is placed down for the membrane to adhere to or to reduce your risk of fasteners backing out and causing damage. The membrane can then be attached by either being ballasted, mechanically fastened or chemically adhered. Membranes are manufactured in sheets and will need to be rolled up and taken to the project site. The membrane sheets are then applied to overlap each other to ensure no exposed roof. They are then typically hot air welded together at the seams. These sheets are quite strong, providing on-roof durability and protection from weather and “wind driven missiles.” They are also very reflective and most achieve an Energy Star and CRRC rating. When you see roofing failures on membrane roofs, it typically happens at seams or flashings. The seams that run the length of the roof are oftentimes weak points and allow water intrusion. This normally occurs when the installers fail to achieve a good weld with adequate bleed out (depending on if it is TPO or PVC). This can happen when the membrane is not welded at a hot enough temperature to ensure a tight weld.
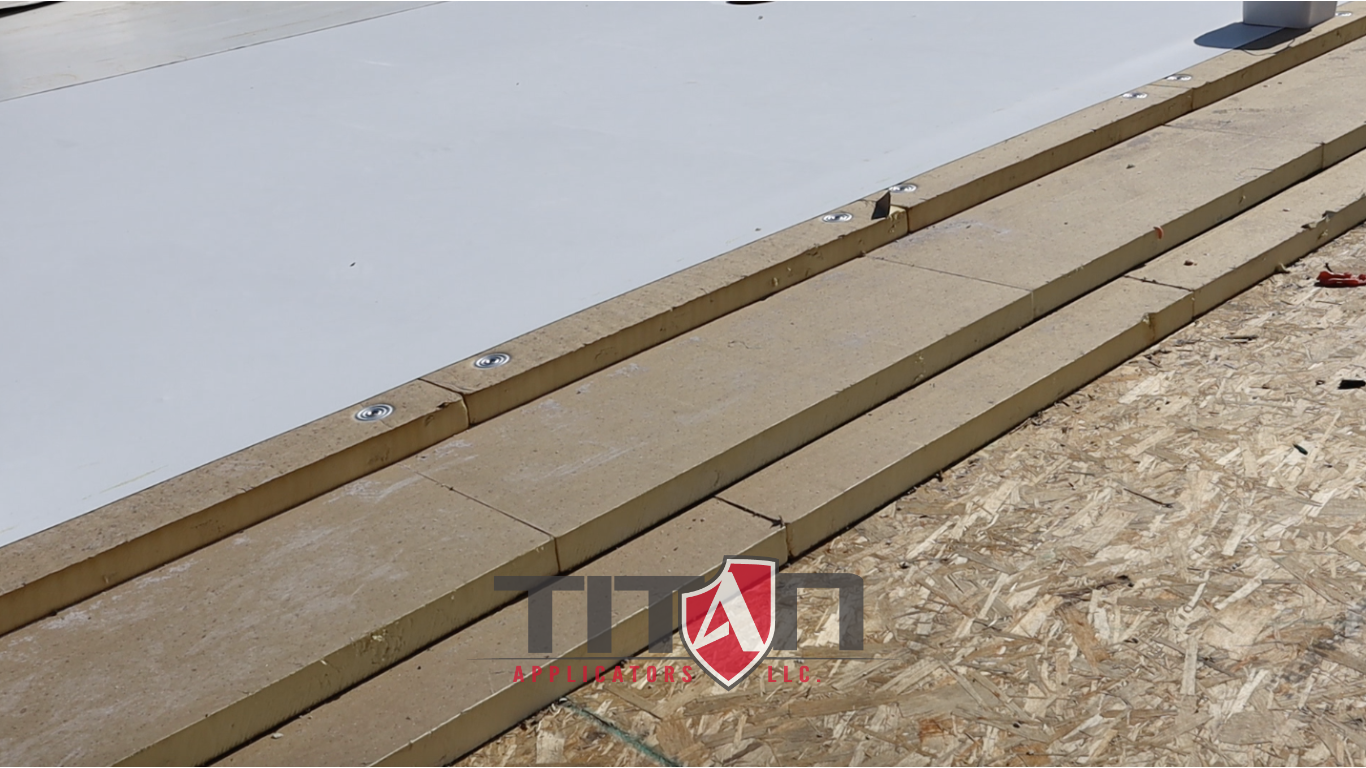
As stated above, the biggest difference between the two roofs comes down to the manufacturing and installation process of the chosen roofing systems. With foam ultimately being manufactured in the field, it does offer a lot of added benefits as listed above. With that being said, because the contractor is ultimately manufacturing it, in the field, out of a controlled setting, it does allow room for a lot more variables. Proper knowledge and training is an absolutely essential piece when it comes to the success of the foam. Because membrane roofing is more so being installed rather than manufactured, it does allow for a more controlled and consistent application. As always, it truly comes down to making sure the right roof is chosen for your circumstances and that the installer is knowledgeable in their trade. If those two things aren’t present on every project, it doesn’t matter if it is SPF or membrane roofing, you will have a failure every time