Since the original publication of this blog post in 2020, the world of roofing continues to face challenges. Supply chain issues, labor shortages, freight, geo-political conflicts, and much more continue disrupt the cost of spray foam and roofing materials alike; sometimes causing changes even by the day. As supply tightens, the challenges will only get worse before they get better. With that said, spray foam roofing materials seem to be more readily available than most other types of roofs. We truly appreciate the working relationships that we have fostered with old and new clients and we are determined to help ensure the success of their roofing projects in these trying times.
Fore the most accurate and up-to-date cost information, please call us directly.
Spray Polyurethane Foam (SPF) roofing is one of the most technologically advanced roofing systems available today. SPF roofing is different than many contemporary roofing systems because it is essentially manufactured on the job site and spray applied in place, versus being mechanically attached.
The average cost of spray foam roofing is between $5.00 to $8.00 per square foot (or $400 to $700 per square) with general material and labor included.
Nonetheless, there are several key factors that influence the final cost of a spray applied foam roof and in this article we will break-down each one.
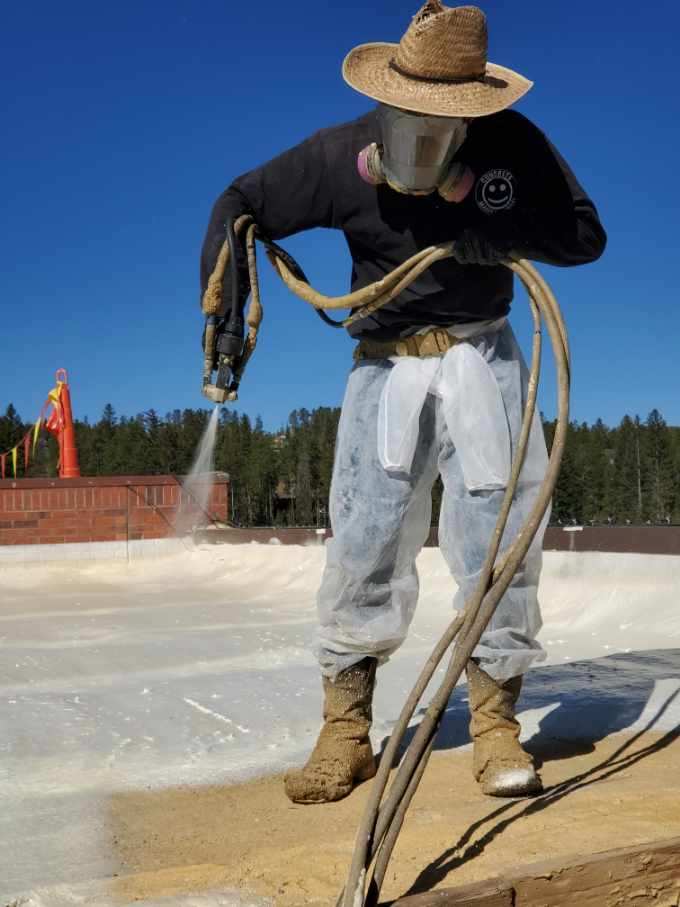
What Determines The Cost of a Spray Foam Roof?
- Knowledge - A quality SPF roof applicator requires a combination of education, examination and experience that will meet or exceed a standard of excellence in the commercial roofing industry. It takes the technical knowledge of a chemist, acuity of the manufacturing process, the business executive expertise in sales, project management and client relations, and, most importantly, it takes determination and drive to out all those elements together to produce a superior spray polyurethane foam roof system. Truly skilled spray foam professionals will never undervalue their worth because their knowledge will attest to their qualifications and competency. If the application and workmanship are of poor quality, then the system will not perform as expected.
- Safety - In the commercial roofing industry, there are two ways to do things: safely or unsafely. At Titan Applicators, safe is the only option. It protects the lives of our team members, it protects the lives of the building occupants, and it protects our clients and us from unnecessary risk exposure. But the fact of the matter is that being safe and complying with OSHA guidelines comes with a slight cost.
- Surface - The combination of SPF and coverings produces a very effective, protective, and water resistant roofing system over almost all existing roof systems. Prior to the application of any spray polyurethane foam, the condition of the surface must be inspected to ensure it is clean and free of moisture or other contaminants. Abnormally high levels of levels cleaning and prep work may result a higher cost to the client. Furthermore, any moisture must be completely removed from on, and in, the substrate. Moisture related labor, such as removal of saturated roof material, will effect the price.
- Roof Size - Spray foam is faster and easier to install because it is sprayed in place and adheres to the substrate as a seamless, lightweight, and self-flashing product. As a result, you will see a huge savings per square foot when compared to other roofing systems. But, roof size will still play a role during the bidding process. Factors are: Material & equipment logistics and mobilization, material transport, etc.
- Covering - A spray foam roof is a great water barrier to protect your commercial building from the harsh Colorado weather but it performs poorly against Ultraviolet (UV) light. As a result, the foam must be protected from the UV light by covering it with a protective layer. One option for a UV protective covering is a spray applied roof coating. The type of coating (typically acrylic or silicone) affect the final cost of the spray foam roofing system. Furthermore, we prefer to embed granules into our coating to increase its overall durability. That can also effect upfront costs. Finally, another protective covering option for a spray foam roof is crushed gravel. The EnduraRock Premier Roofing system, by NCFI, is incredibly resilient to Colorado weather, easy to maintain and is our personal favorite commercial roofing system. The down side - not all roofs qualify for foam & gravel.
- Thickness - Spray polyurethane foam applications are typically figured by the "board foot." A board foot is a unit of measurement for the volume of one foot in length by one foot in width by one inch in thickness. The average board foot cost of one inch of roofing foam is around $2.25. Thus, a two inch application of closed-cell roofing foam can cost around $5.50 per square foot. Case-in-point = The thicker the foam, the higher the cost!
- Warranty - Without getting into the details of good warranties & bad warranties (and who is backing them up), a foam roof warranty can effect the final cost of a commercial roofing project by summing it up like this: the longer the warranty, the more expensive it will be. [Especially if the contractor and manufacturer are worth a darn.]
Why Use Spray Foam On A Commercial Roof?
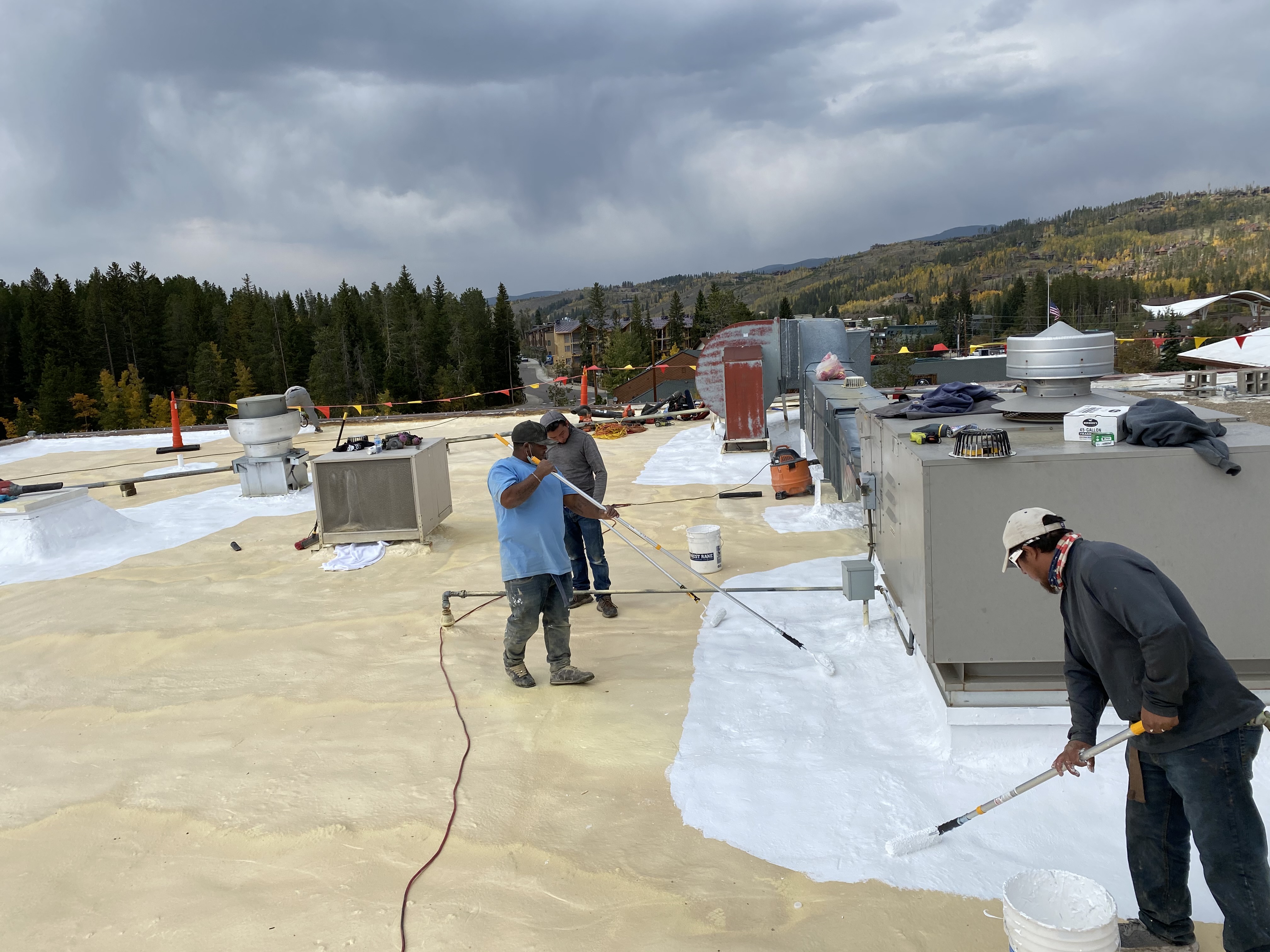
What's the cost of a spray foam roofing system in 2022?
To date, Titan Applicators is the only NCFI Tier One Certified Roofing Contractor in the state of Colorado. Our team has demonstrated competence with the technical application of spray polyurethane foam roofing, troubleshooting of SPF foam application equipment, experience, knowledge of roofing characteristics and building codes, and financial stability.
Why do we bring this up? Because we want to be the best and NCFI holds us to accountable to that. To be considered for Tier One status, and to maintain it, NCFI has a comprehensive list of requirements that we must uphold before, during & after a roofing application. - They don't just hand out contractor certifications after a 2-day crash course and they don't hesitate to say "no" to a contractor when he or she does not qualify.
So, what is a fair price for an SPF roof system? Well, we still haven't encountered a client who wants to pay us for more than what we're asking. Everyone wants a good deal. But, as Ben Franklin wisely put it: "The bitterness of poor quality remains long after the sweetness of low price is forgotten."
Spray foam roofs can save up front costs because they are faster install, require less manpower, and cause less interruption to building operations. Long term costs are greatly reduced because spray foam roofs are easier to maintain and can significantly reduce a building's energy consumption. But, regardless of what type of roof you put on your commercial building, an unqualified commercial roofing contractor is much more expensive than one that is qualified because you're paying to have your roof worked on more than once. - That's where Titan Applicators excels.